Fabric8 Membrane Services designs and manufactures textile products that are used in a wide range of industries and applications. Our employees cut and sew intricate fabric and membrane to exact specifications to meet the particular demands of our clients. We provide a high-quality, traceable, and consistent manufacturing environment for clients that require the creation of textile products.
Learn more about Fabric8 here!
As part of the Fabric8 integrated approach, we go back to the science of the underlying fabric to alter the materials to meet the unique performance requirements of the final product while taking installation location, weather, and landscape into consideration.
In this blog, we walk through the entire fabrication process to give you a “bird’s eye” view of what we do and how we do it here at Fabric8.
DESIGN & TEMPLATES
Our Technical Team has its own office and facilities, as well as extensive industry experience in the production of bespoke textile components for a wide range of complicated and specialized applications.
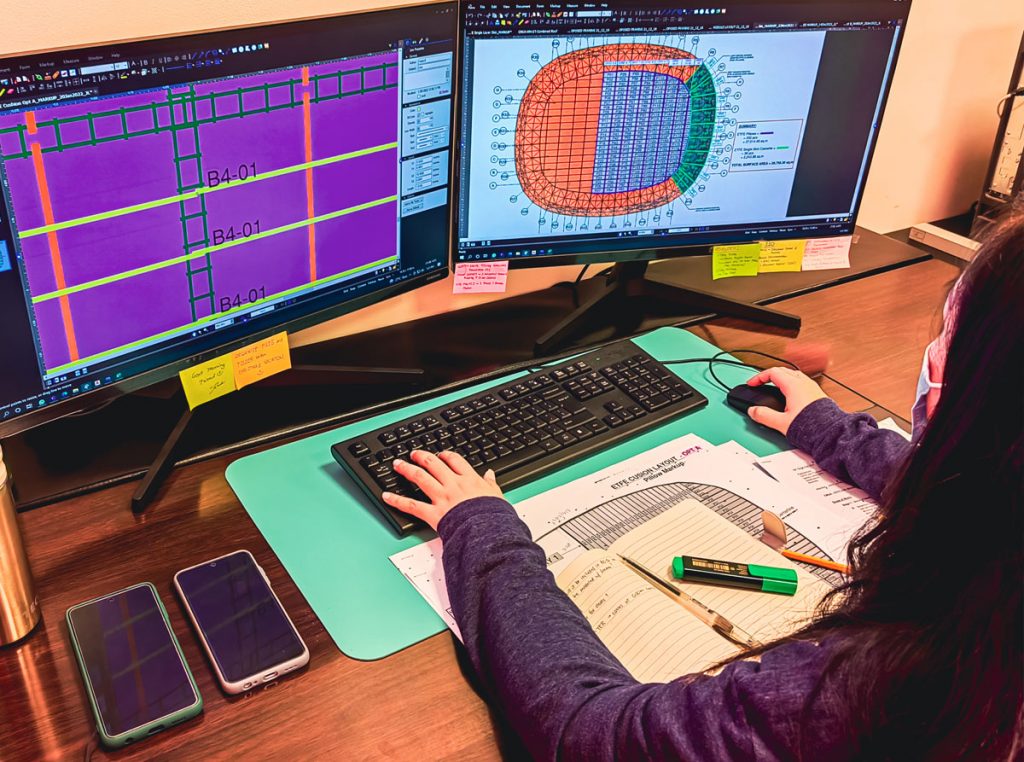
We deal with pre-approved designs and patterns ranging from modest shade structures, curtains and panels to large fabric buildings and stadiums. We also assist our customers in developing a viable specification that includes drawn designs and templates for unique bespoke parts as well as their special needs.
MEASURING & CUTTING
Fabric8 utilizes a Strength Test Machine to guarantee that the quality strength of the fabric to be used fulfills national standards as well as the specific requirements of our clients, taking into consideration the landscape and placement for the fabricated material.
Our CNC (Computer Numeric Control) machine is used for prototyping and full production cutting. We can cut practically any type of fabric into almost any shape. Electronic templates and cutting patterns may be programmed and kept in memory before being instantly retrieved for quick project turnaround with little set-up time.
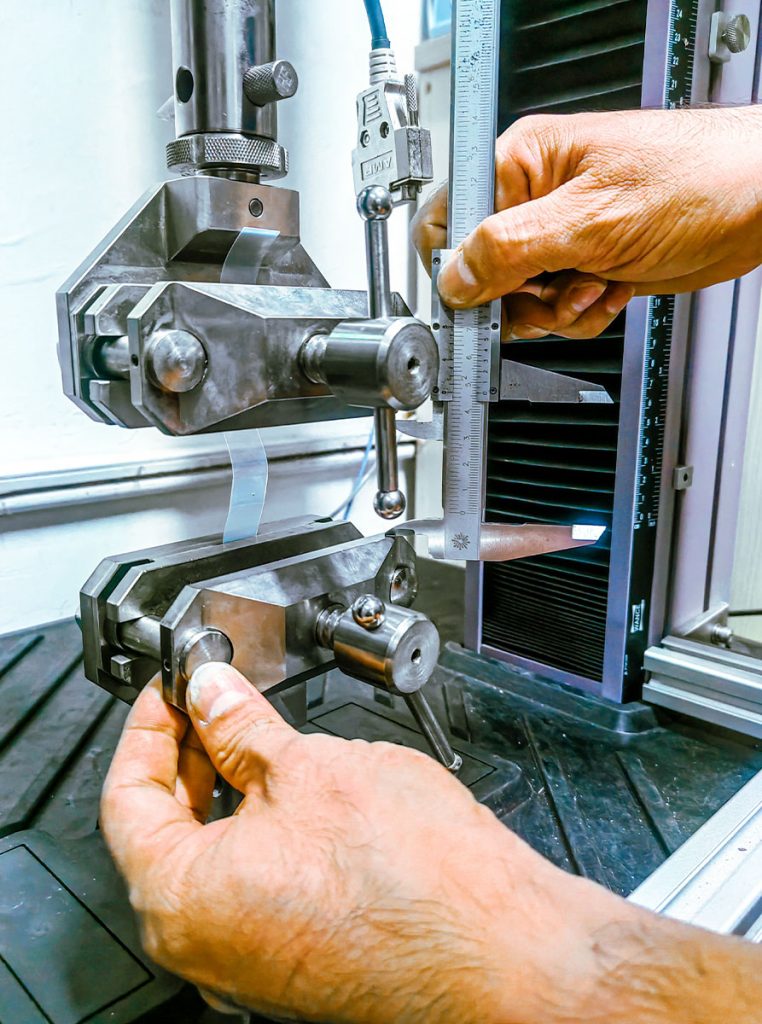
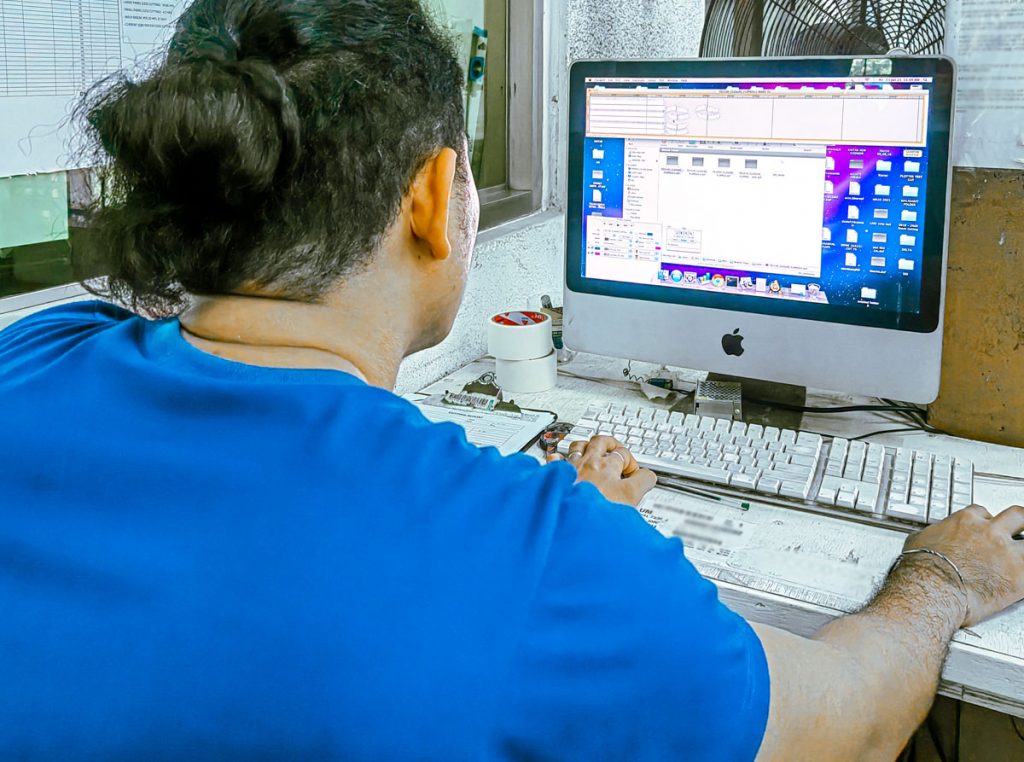
Cutting patterns may be nested for optimal efficiency with the built-in software. This reduces fabric waste and saves money by avoiding manual handling errors. Because the CNC machine cuts without damaging the surrounding fibers, it produces a high-quality solid edge. This is due to the contactless method of cutting which reduces the physical manipulation of the material.
We utilize this flexible manufacturing technique to create one-off pieces for prototype, testing, or bespoke applications, as well as scalable and cost-effective full-length production runs.
ASSEMBLY
We have professional staff of machinists that are highly skilled in the fabrication of technical fabric textiles using heavy-duty welding, abrading, and sewing equipment.
Sewing
We also have an in-house sewing station where our team can stitch textile fabric with other materials, ie. velcro, mag fan cover, pull tabs etc.
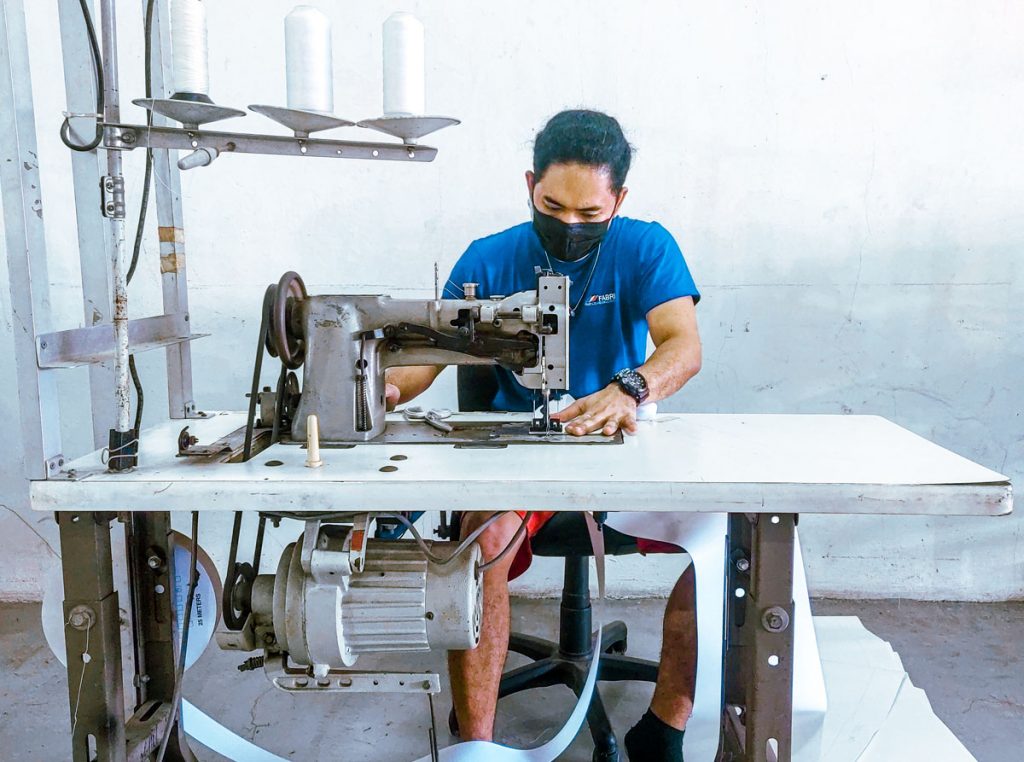
Abrading
Grinding and polishing surfaces by eliminating entire parts of the material substrate is the abrasive process. It is described as the wearing away of a material's surface at high levels owing to friction. It is a technique for truing and leveling the surface of a substrate during the finishing process or when two fabrics are bonded into one.
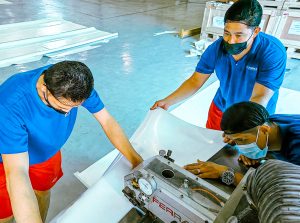
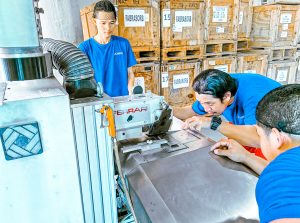
Welding
High-frequency welding (also known as HF welding or RF welding) is an industrial procedure that uses an induced emf to join two plastic pieces. The resulting joint can be extremely strong, oftentimes exceeding the initial strength of materials connected. In rare cases, the weld would be stronger than that of the original materials.
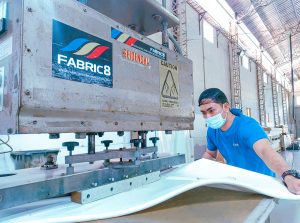
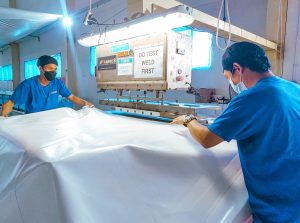
The Continuous Welding technique and objective are the same as with HF, but our continuous welding equipment covers a much larger area of an entire linear fraction of fabric, making it possible to weld in a straight and wider portion.
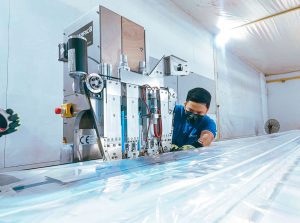
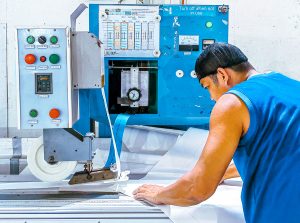
Tensile Heat Tacking & Hole Punching
Fabric textile tacking is used for initial fabric fastening to make sure that the products are intact and ready for accurate welding. Depending on the nature of a project, hole punching is typically employed to provide fabric tension, an access point for ropes for strength and manual adjustability.
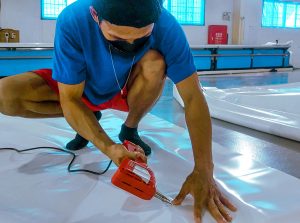
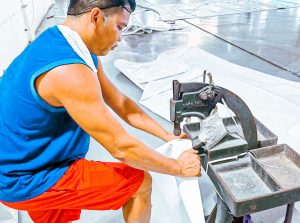
Our technical expertise gives us an edge to be successful in developing particular work methods and guidance processes that help consistent procedures for highly complex commercial/industrial textile assemblies.
FREIGHT & DELIVERY
The final product is then shipped to our clients, and one thing we do is build safe containers to guarantee that the client receives an undamaged and secure product.
Transporting products from an original location to a designated destination is an important part of the process. Delegating our hard work to our trusted freight logistic carriers is critical to ensure that the final fabric product is delivered to our clients in excellent form and condition.
To ensure that everything arrives to the customer in great shape and that our clients’ needs are both met and exceeded, our deliveries are transported in a solid, secure manner. At Fabric8, we have developed our own design for solid timber packaging, that is made in-house to guarantee the highest quality for every shipment.